Revealing the Intricacies of Fasteners and Machining Procedures for Optimal Efficiency
In the world of design and production, the selection of bolts and the ins and outs of machining processes play a crucial duty in figuring out the best performance and resilience of a product. From the apparently straightforward job of picking the best kind of bolt to the complex accuracy machining techniques used, every action in this procedure demands careful interest to detail. As we start this exploration right into the world of bolts and machining, we will certainly discover the subtle yet essential aspects that can substantially influence the performance and top quality of the end product, shedding light on the often overlooked aspects that can make all the distinction in achieving optimal performance.

Relevance of Correct Bolt Option
Selecting the proper fasteners is critical in making sure the architectural honesty and long life of any mechanical setting up. Bolts play a fundamental function in holding elements with each other securely, with the best option adding substantially to the total performance and dependability of the assembly. When picking fasteners, aspects such as product compatibility, ecological conditions, load-bearing ability, and simplicity of installment need to be thoroughly considered to guarantee optimum efficiency.
Inappropriate fastener option can lead to a variety of problems, including helping to loosen, corrosion, and also structural failing. Using fasteners that are not matched to the certain demands of the assembly can endanger its performance and position safety risks. As a result, engineers and developers need to thoroughly evaluate the application requires and pick fasteners that meet or surpass the essential standards and requirements.
Furthermore, the correct bolt choice process includes examining the joint design, prepared for lots, vibration degrees, and potential thermal growth or contraction to make certain that the selected fasteners can endure the operating problems properly. By focusing on correct fastener choice, producers can improve the high quality, resilience, and efficiency of their mechanical settings up.
Kinds and Characteristics of Fasteners
An essential facet of mechanical settings up lies in comprehending the diverse kinds and one-of-a-kind characteristics of bolts utilized in various industrial applications. Bolts are critical parts that hold structures together, ensuring security and functionality.
Screws are threaded fasteners that are generally utilized to join 2 or even more parts together. Nuts are inside threaded bolts that mate with bolts to hold elements together. Washers are slim plates that disperse the lots of a fastener, preventing damages to the product being secured.
Recognizing the features of each type of bolt is crucial for choosing the right one for a particular application, ensuring optimal performance and integrity of the mechanical setting up. Fasteners and Machining.
Accuracy Machining Strategies for Efficiency
The detailed layout requirements of different fasteners necessitate utilizing precision machining techniques for optimal efficiency in making processes. Accuracy machining is essential in making sure that bolts meet the exact specs required for their intended application. One of the key strategies made use of in accuracy machining is Computer Numerical Control (CNC) machining, which allows high degrees of accuracy and repeatability in the manufacturing of fasteners. CNC machines are capable of executing complicated cuts and shaping procedures with marginal human intervention, causing raised effectiveness and consistency in the manufacturing process.
In addition to CNC machining, other accuracy methods such as grinding, milling, and turning are generally made use of to achieve the limited tolerances required for bolts. These techniques allow makers to develop bolts with smooth surfaces, exact measurements, and high structural honesty. By using precision machining methods, makers can improve the quality of fasteners, lower product waste, and improve general production effectiveness. The use of advanced machining processes assists guarantee that bolts satisfy market standards and customer expectations for performance and dependability.
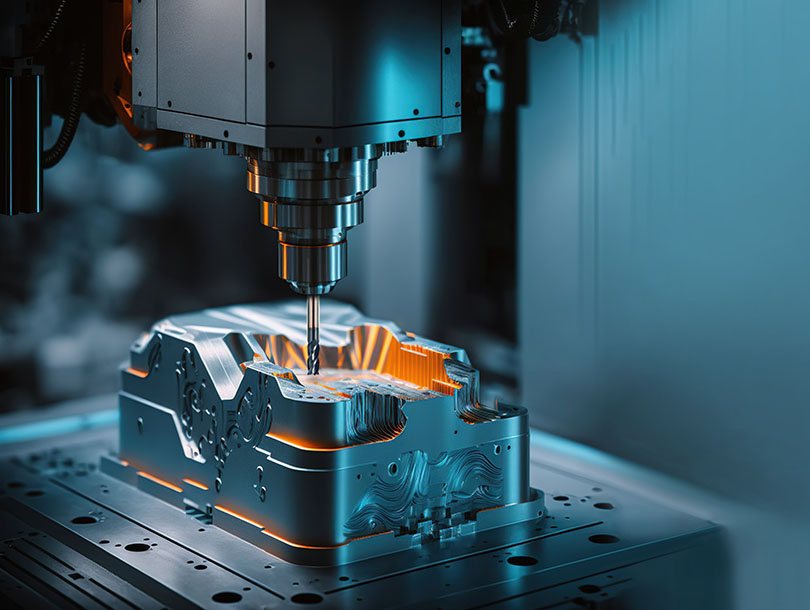
Factors Influencing Machining Process Performance
Numerous variables play a substantial function in establishing the efficiency of machining processes in the manufacturing of bolts. Maximizing these criteria based on the details needs of the fastener being generated is crucial to achieving precise and cost-efficient machining.
Maker rigidness and stability likewise play a vital duty in establishing machining process efficiency. A secure machine with very little vibrations can boost precision and avoid tool wear, resulting in much better total performance. The ability and experience of the equipment operator can not be undervalued. An experienced driver can make real-time adjustments, troubleshoot problems effectively, and guarantee that the machining procedure runs smoothly, ultimately affecting the last high quality of the bolt.

Top Quality Control Actions in Manufacturing
Elements affecting machining procedure performance, such as reducing device selection and maker stability, straight influence the execution of quality assurance procedures in manufacturing. Quality control actions are crucial in making certain that items meet the required criteria and read what he said requirements. In the manufacturing procedure, numerous techniques are utilized to preserve quality criteria. Assessment and testing play an important role in recognizing any type of discrepancies from the preferred result. Regular upkeep of machining devices is likewise vital to maintain top quality control. Calibration of helpful resources devices and equipments is required to guarantee accurate and precise manufacturing procedures. Additionally, carrying out standardized operating procedures and protocols can help in maintaining uniformity and top quality throughout the production line. Quality control measures not only concentrate on completion product however likewise on every phase of the production procedure to avoid flaws and errors. By sticking to rigid high quality control procedures, manufacturers can enhance client contentment, construct a reputation for integrity, and inevitably accomplish ideal performance in their machining procedures.
Conclusion
In verdict, picking the appropriate fasteners and making use of precision machining strategies are necessary for optimum performance in making procedures. Understanding the types and features of fasteners, in addition to factors affecting machining procedure efficiency, can bring about improved efficiency and quality control procedures. By focusing on these intricacies, producers can attain greater levels of efficiency and reliability in their items.
In the realm of design and production, the option of fasteners and the complexities of machining procedures play an essential duty in figuring out the supreme efficiency and sturdiness of a product discover this info here (Fasteners and Machining). One of the main strategies used in precision machining is Computer Numerical Control (CNC) machining, which allows high degrees of accuracy and repeatability in the production of bolts. The use of advanced machining processes helps make certain that fasteners satisfy market standards and consumer expectations for performance and reliability
In conclusion, choosing the ideal fasteners and utilizing precision machining techniques are necessary for optimum efficiency in making procedures. Recognizing the kinds and features of bolts, along with variables affecting machining procedure performance, can lead to improved effectiveness and top quality control measures.